Introducing the Art of Aluminum Spreading: A Comprehensive Overview for Beginners
In the realm of metalworking, aluminum casting stands as a craft that marries virtuosity with accuracy. Recognizing the nuances of this old method can be both interesting and rewarding, specifically for those venturing right into the globe of casting for the very first time. As newbies get started on this journey, they are encountered with a labyrinth of methods, tools, and security procedures that form the structure of understanding the art of light weight aluminum casting. This thorough overview aims to demystify the process, providing a roadmap that browses with the history, essentials, safety measures, actions, and alloys important for those looking for to create their very own aluminum castings.
History of Light Weight Aluminum Spreading
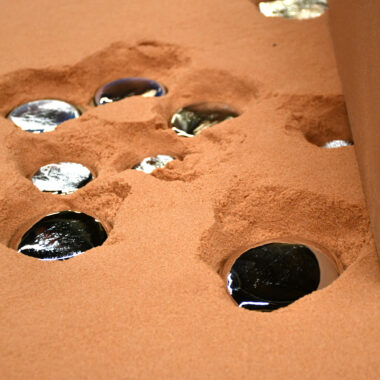
One of the key milestones in the history of aluminum casting was the creation of the first aluminum spreading machine in 1886 by Charles Martin Hall. This advancement transformed the industry by enabling mass manufacturing of aluminum spreadings, leading the way for its prevalent use in various fields such as automobile, aerospace, and building. Over the years, developments in technology have actually better fine-tuned the aluminum casting process, making it more exact, affordable, and eco pleasant. Today, light weight aluminum spreading remains to play an essential duty in the manufacturing field, offering a flexible service for creating intricate parts with high strength and sturdiness.
Crucial Devices for Newbies
When beginning on the trip of aluminum spreading as a beginner, acquiring the necessary tools is paramount for guaranteeing a successful and smooth casting procedure. A crucible, commonly made of graphite or clay-graphite, is basic for thawing light weight aluminum. Crucible tongs are essential for managing the hot crucible safely. A furnace, either electrical or gas-powered, is crucial for thawing the aluminum to its fluid state. To get rid of contaminations and solidified particles, a skimming device is vital. A stirring pole helps in mixing the liquified light weight aluminum and making certain harmony. Flask and molding sand are essential for developing mold and mildews into which the liquified light weight aluminum is put. A mold frame, containing deal and drag, is needed for molding the sand. Airing vent poles assist in creating networks for air and gas to escape from the mold and mildew throughout casting. Security equipment such as heat-resistant gloves, apron, and face guard are critical for shielding oneself during the casting process. With these important devices in hand, newbies can start their light weight aluminum casting journey with confidence.
Basic Action In Light Weight Aluminum Spreading
To start the light weight aluminum spreading process successfully, beginners have to first prepare the mold and ensure its proper placement within the mold and mildew structure - aluminum casting illinois. It is vital to permit the light weight aluminum sufficient time to strengthen and cool inside the mold before trying to get rid of the spreading.
After the aluminum has cooled down and solidified, the mold and mildew needs to be opened to expose the recently developed casting. Understanding these standard actions is vital for newbies looking to dive right into the art of light weight aluminum casting.
Typical Types of Aluminum Alloys
One of the crucial considerations in light weight aluminum casting is comprehending the varied series of aluminum alloys typically made use of while doing so. Light weight aluminum alloys are classified based upon their chemical make-up and homes, with each kind offering special features fit for different spreading applications. One common aluminum alloy is A356, recognized for its excellent castability and excellent mechanical residential or commercial properties, making it preferred in various sectors such as automobile and aerospace. An additional commonly made use of alloy is 6061, valued for its high strength and corrosion resistance, making it suitable for aquatic applications and structural components. In addition, the 380 alloy is preferred for its premium fluidity and article machinability, making it a top selection for complex castings requiring elaborate details. Recognizing the residential properties and benefits of these usual light weight aluminum alloys is vital for novice casters to select one of the most appropriate alloy for their details casting demands, ensuring top quality end results in their casting projects - aluminum casting illinois.
Safety Precautions in Spreading Light Weight Aluminum
Taking into consideration the crucial duty of aluminum alloys in the casting procedure, prioritizing safety and security preventative measures is extremely important to ensure a efficient and safe and secure spreading atmosphere. When dealing with molten aluminum, it is critical to wear ideal individual safety devices (PPE) such as heat-resistant gloves, aprons, face guards, and safety and security goggles to prevent burns and injuries. Additionally, guarantee appropriate ventilation in the casting area to minimize exposure to unsafe fumes and gases launched throughout the melting process.
To stop possible fires, always have a fire extinguisher neighboring and develop a clear emptying strategy in instance of emergencies. It is vital to conduct routine safety and security training sessions for all employees associated with the casting procedure to inform them on finest techniques and emergency procedures. Proper handling of devices, including crucibles, ladles, and mold and mildews, is vital to stop mishaps and keep a safe functioning setting.
Furthermore, maintaining a orderly and clean office can help in reducing the danger of slides, journeys, and drops. By adhering to these safety and security precautions, beginners can create a safe foundation for mastering the art of light weight aluminum spreading.
Verdict
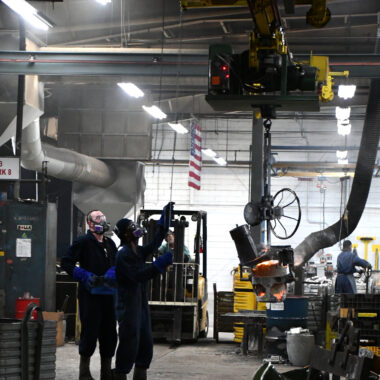
It was not until the 19th century that significant improvements in aluminum spreading were made, particularly with the growth of extra pop over to these guys effective methods for melting and forming light weight aluminum alloys.
One of the key milestones in the background of aluminum spreading was the creation of the very first light weight aluminum casting equipment in 1886 by Charles Martin Hall.When beginning on the journey of light weight aluminum spreading as a newbie, getting the necessary tools is extremely important for guaranteeing a smooth and successful casting process.One of the key considerations in aluminum spreading is understanding the diverse variety of light weight aluminum alloys commonly used in the procedure. By understanding the standard steps and necessary tools entailed in light weight aluminum spreading, beginners can successfully function with various types of light weight aluminum alloys.
Comments on “Aluminum Casting Illinois: Unrivaled Durability, Unbeatable Rates”